Crane Daily Inspection & Maintenance Checklist
As critical assets in construction and manufacturing industries, cranes demand rigorous daily checks and systematic maintenance to prevent accidents and ensure operational efficiency. This comprehensive guide outlines proven strategies to extend crane lifespan while complying with OSHA/ISO safety standards.
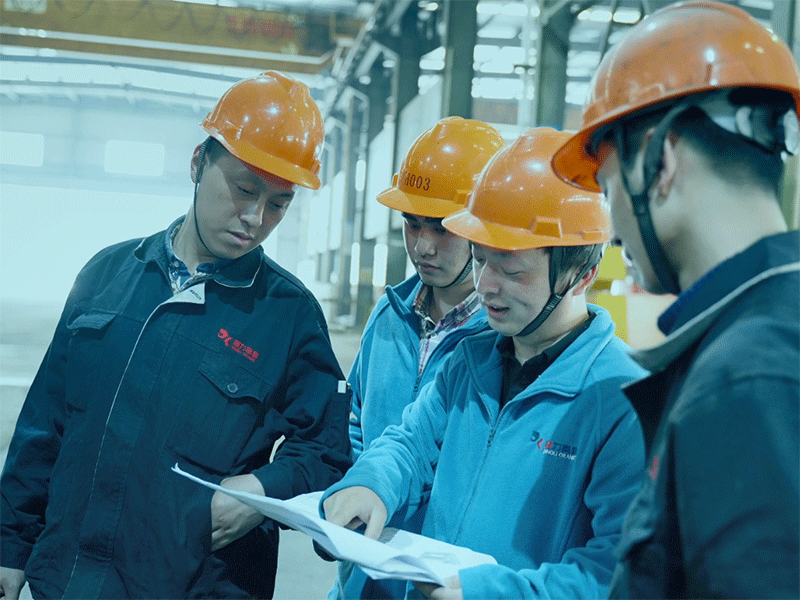
I. Pre-Shift Inspection Checklist (Mandatory Daily Tasks)
1. Structural Integrity Verification
Inspect booms, outriggers, and load-bearing welds for cracks/corrosion (Use NDT methods if suspected)
Confirm all bolts/pins are properly torqued (Refer to manufacturer's torque specs)
Clear debris from tracks/wheels and check tire pressure (±5% of recommended PSI)
2. Safety System Validation
Test overload limiter with 110% load simulation (Audit automatic cut-off function)
Verify limit switches for hoist/trolley travel (Maintain 3ft buffer from endpoints)
Conduct emergency stop test (Full stop within 0.5 seconds at no-load condition)
3. Electrical & Control Diagnostics
Check control panel for loose connections/arc marks (Thermal imaging recommended quarterly)
Calibrate remote controller response time (<0.2s delay)
Ensure alarms (wind speed/anti-collision) are fully operational
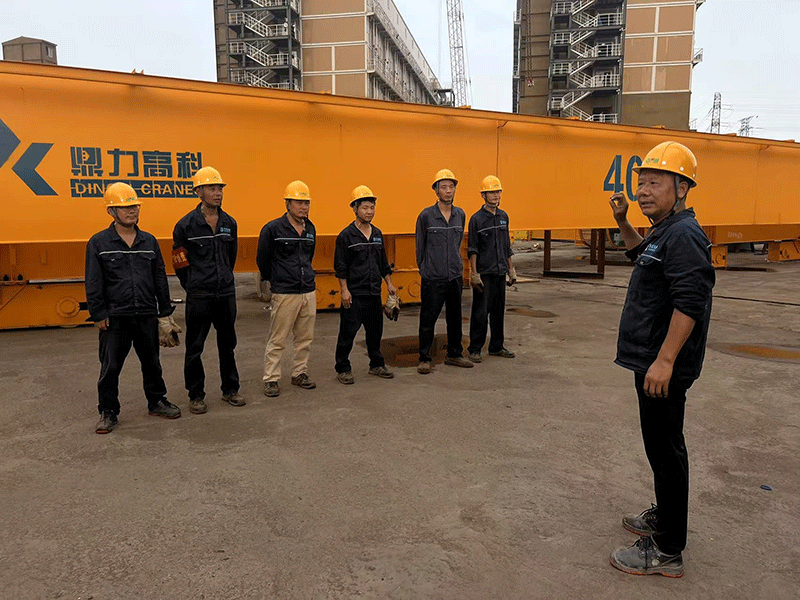
II. Scheduled Maintenance Program
1. Lubrication Management
Weekly: Apply ISO VG 68 grease to slew bearings and wire rope sheaves
Monthly: Degrease & re-lubricate hoist gearboxes (Follow OEM viscosity charts)
Wire Rope Care: Replace if 6×19 strand shows >12 broken wires in 30xD length
2. Component Overhaul Cycles
Quarterly:
Measure brake lining thickness (Replace at <3mm remaining)
Conduct hydraulic oil analysis (ISO 4406 code ≤18/16/13)
Annually:
Perform 125% static load test (ASTM E4 standards)
Laser-align runway rails (<±5mm deviation per 10m)
III. 5 Proactive Maintenance Strategies
Environmental Adaptations
Coastal sites: Apply zinc-rich epoxy coatings (Salt spray resistance >500hrs)
Arctic zones: Switch to synthetic lubricants (-40°C pour point)
Predictive Analytics
Install IoT vibration sensors (Alert on 4-6mm/s RMS anomalies)
Log hour-meter data to schedule part replacements (e.g., contactors @ 100k cycles)
Operator Training
Ban shock loading practices (Max acceleration <0.3m/s²)
Require annual certification refreshers (ANSI/ASME B30.2 compliance)
Spare Parts Optimization
Stock critical components: Limit switches, hydraulic seals, sheave bearings
Partner with certified suppliers (24/7 emergency delivery guarantee)
Third-Party Audits
Schedule LEEA-certified inspections (Includes SWL deration calculations)
IV. Next-Gen Maintenance Technologies
AI-Powered Diagnostics: Machine learning algorithms predict bearing failures 14 days in advance (90% accuracy)
Augmented Reality (AR): Overlay maintenance instructions via smart glasses (Reduce repair time by 35%)
Blockchain Recordkeeping: Immutable service history for compliance audits
Conclusion
Implementing this crane maintenance protocol can reduce unplanned downtime by 40-60% and lower repair costs by 30%. For a personalized maintenance plan or certified inspection services, contact our crane safety specialists today.